5 Mobile Fastener Tips
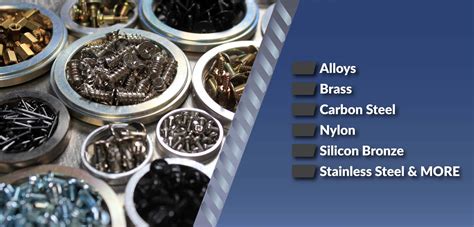
Mobile fastening is a critical aspect of various industries, including construction, automotive, and manufacturing. The ability to securely and efficiently fasten materials on-site or in mobile environments is essential for ensuring the quality and durability of the final product. With the advancements in technology and the increasing demand for mobility, mobile fastening solutions have become more sophisticated, offering a range of benefits from improved productivity to enhanced safety. In this article, we will delve into five key mobile fastener tips, providing insights into the best practices, tools, and techniques for achieving optimal results in mobile fastening applications.
Key Points
- Choosing the right mobile fastening tool based on the application and material requirements
- Understanding the importance of proper fastener selection for mobile applications
- Implementing safety measures to prevent accidents and injuries during mobile fastening
- Optimizing mobile fastening processes for improved efficiency and productivity
- Maintaining and troubleshooting mobile fastening equipment for prolonged lifespan and reliability
Choosing the Right Mobile Fastening Tool

The first step in achieving successful mobile fastening is selecting the appropriate tool for the job. The choice of tool depends on several factors, including the type of material being fastened, the environment in which the fastening is taking place, and the desired level of automation. For instance, pneumatic tools are often preferred for heavy-duty applications due to their high torque output and durability, while cordless tools offer greater flexibility and convenience for jobs that require frequent relocation. It is essential to consider these factors and match them with the capabilities of the tool to ensure efficient and effective fastening.
Fastener Selection for Mobile Applications
The selection of the right fastener is equally crucial as choosing the appropriate tool. Different materials and applications require specific types of fasteners to ensure a secure and lasting bond. For example, stainless steel fasteners are ideal for applications where corrosion resistance is a priority, while aluminum fasteners are preferred for their lightweight and high strength-to-weight ratio. Understanding the properties and applications of various fasteners is vital for making informed decisions that meet the project’s requirements and specifications.
Fastener Material | Properties | Applications |
---|---|---|
Stainless Steel | Corrosion-resistant, high strength | Marine, chemical processing, medical equipment |
Aluminum | Lightweight, high strength-to-weight ratio | Aerospace, automotive, construction |
Brass | Corrosion-resistant, low friction | Hardware, fixtures, electrical components |

Implementing Safety Measures

Safety is a paramount concern in any fastening operation, and mobile fastening is no exception. The dynamic nature of mobile environments, where workers may be using powerful tools in confined or open spaces, necessitates the implementation of stringent safety protocols. This includes wearing personal protective equipment (PPE) such as gloves, safety glasses, and ear protection, as well as ensuring that the work area is clear of debris and obstacles. Furthermore, regular tool maintenance and operator training are critical for preventing accidents and ensuring that the fastening process is conducted safely and efficiently.
Optimizing Mobile Fastening Processes
Optimization of mobile fastening processes is key to improving efficiency and productivity. This can be achieved through various means, including the use of ergonomically designed tools that reduce operator fatigue, implementing quality control measures to minimize errors and rework, and leveraging technology such as mobile apps and software solutions to streamline workflow and data management. By focusing on process optimization, businesses can significantly reduce costs, enhance product quality, and improve customer satisfaction.
Maintenance and Troubleshooting
The maintenance and troubleshooting of mobile fastening equipment are essential for ensuring the longevity and reliability of the tools. Regular maintenance tasks, such as cleaning, lubricating, and checking for wear and tear, can prevent downtime and extend the lifespan of the equipment. Additionally, understanding common issues and having a structured approach to troubleshooting can help in quickly identifying and resolving problems, thereby minimizing the impact on productivity and project timelines.
What are the most common safety hazards in mobile fastening operations?
+The most common safety hazards include tool accidents, falls, and being struck by moving objects. Proper training, use of PPE, and adherence to safety protocols can significantly reduce these risks.
How can I improve the efficiency of my mobile fastening process?
+Improving efficiency can be achieved by optimizing tool selection, implementing process streamlining measures, and utilizing technology to manage workflows and data. Regular training and maintenance of equipment also play a critical role.
What factors should I consider when choosing a fastener for a mobile application?
+Key factors include the type of material being fastened, environmental conditions, the required strength and durability of the fastener, and compatibility with the fastening tool. Consulting with a professional or referring to industry guidelines can provide more detailed insights tailored to specific applications.
In conclusion, mobile fastening is a complex process that requires careful consideration of tool selection, fastener choice, safety protocols, process optimization, and maintenance. By following these five mobile fastener tips and staying informed about the latest developments in technology and best practices, professionals can enhance their mobile fastening operations, leading to improved productivity, quality, and safety. Whether in construction, manufacturing, or another industry, the right approach to mobile fastening can make a significant difference in project outcomes and business success.