5 T Mobile Warehouse Tips

When it comes to managing a T-Mobile warehouse, efficiency and organization are key to ensuring seamless operations and meeting customer demands. With the rise of e-commerce and the increasing importance of fast and reliable shipping, warehouses play a critical role in the supply chain. In this article, we will explore five essential tips for optimizing T-Mobile warehouse operations, focusing on inventory management, storage solutions, workforce management, technology integration, and performance metrics.
Inventory Management Strategies
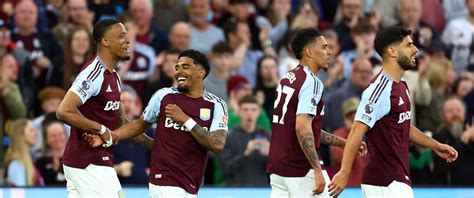
Effective inventory management is the backbone of any successful warehouse operation. For T-Mobile warehouses, this involves implementing a robust inventory tracking system that can accurately monitor stock levels, track shipments, and predict demand. One strategy is to adopt a just-in-time (JIT) inventory system, which ensures that products are received and shipped out quickly, minimizing storage costs and reducing the risk of inventory obsolescence. According to a study by the National Retail Federation, companies that implement JIT inventory systems can reduce their inventory costs by up to 20%.
Implementing a First-In-First-Out (FIFO) System
A FIFO system ensures that older products are shipped out before newer ones, reducing the likelihood of inventory becoming outdated. This is particularly important for T-Mobile warehouses, which handle electronic devices with limited shelf lives. By implementing a FIFO system, warehouses can minimize waste, reduce the need for inventory write-offs, and improve customer satisfaction. For instance, a FIFO system can help ensure that customers receive the latest models of smartphones, which is critical in the fast-paced telecommunications industry.
Inventory Management Metric | Target Value |
---|---|
Inventory Turnover Ratio | 5-7 times per year |
Fill Rate | 95-98% |
Order Cycle Time | 24-48 hours |

Optimizing Storage Solutions
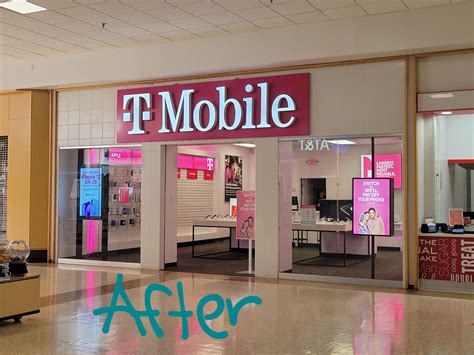
T-Mobile warehouses require flexible and scalable storage solutions to accommodate a wide range of products, from smartphones to accessories. One approach is to use modular shelving systems, which can be easily reconfigured to meet changing storage needs. Additionally, warehouses can utilize vertical storage solutions, such as mezzanines or pallet racks, to maximize storage capacity and reduce floor space. According to a study by the Warehouse Education and Research Council, companies that optimize their storage solutions can increase their storage capacity by up to 30%.
Implementing a Labeling and Signage System
A clear and consistent labeling and signage system is essential for efficient warehouse operations. This includes labeling storage areas, aisles, and products, as well as providing clear signage for workforce members and visitors. A well-designed labeling and signage system can help reduce errors, improve navigation, and enhance overall safety. For example, a labeling system can help warehouse staff quickly identify the location of specific products, reducing the time spent on inventory searches.
Key Points
- Implement a robust inventory tracking system to monitor stock levels and predict demand
- Adopt a JIT inventory system to reduce storage costs and minimize inventory obsolescence
- Utilize modular shelving systems and vertical storage solutions to maximize storage capacity
- Implement a labeling and signage system to improve navigation and reduce errors
- Invest in workforce training and development to improve productivity and efficiency
Workforce Management and Training
Effective workforce management is critical to the success of T-Mobile warehouses. This includes investing in training and development programs that focus on inventory management, storage solutions, and technology integration. By providing workforce members with the skills and knowledge they need to perform their jobs efficiently, warehouses can improve productivity, reduce errors, and enhance customer satisfaction. According to a study by the American Society for Training and Development, companies that invest in employee training can see a return on investment of up to 300%.
Implementing a Performance Metrics System
A performance metrics system can help T-Mobile warehouses track key performance indicators (KPIs) such as inventory turnover, fill rate, and order cycle time. By monitoring these metrics, warehouses can identify areas for improvement, optimize operations, and make data-driven decisions. For instance, a performance metrics system can help warehouses identify bottlenecks in their operations, allowing them to make targeted improvements to increase efficiency.
Performance Metric | Target Value |
---|---|
Inventory Accuracy | 99-100% |
Order Fulfillment Rate | 95-98% |
Shipping Error Rate | <1% |
Technology Integration and Automation
Technology integration and automation are critical components of modern warehouse operations. T-Mobile warehouses can benefit from implementing automated storage and retrieval systems (AS/RS), which can improve inventory management, reduce labor costs, and enhance efficiency. Additionally, warehouses can utilize warehouse management systems (WMS) to streamline operations, improve visibility, and reduce errors. According to a study by the Material Handling Institute, companies that implement AS/RS can reduce their labor costs by up to 50%.
Implementing a Warehouse Management System (WMS)
A WMS can help T-Mobile warehouses manage inventory, track shipments, and optimize operations. By integrating with existing ERP software, a WMS can provide real-time visibility into warehouse operations, enabling data-driven decisions and improving overall efficiency. For example, a WMS can help warehouses optimize their inventory levels, reducing the need for costly inventory write-offs and improving customer satisfaction.
What is the importance of inventory management in T-Mobile warehouses?
+Inventory management is critical to the success of T-Mobile warehouses, as it ensures that products are received, stored, and shipped out efficiently. Effective inventory management can help reduce costs, improve customer satisfaction, and enhance overall efficiency.
How can T-Mobile warehouses optimize their storage solutions?
+T-Mobile warehouses can optimize their storage solutions by utilizing modular shelving systems, vertical storage solutions, and labeling and signage systems. These solutions can help maximize storage capacity, reduce errors, and improve navigation.
What is the role of technology integration in T-Mobile warehouses?
+Technology integration plays a critical role in T-Mobile warehouses, as it enables the implementation of automated storage and retrieval systems, warehouse management systems, and other technologies that can improve efficiency, reduce errors, and enhance customer satisfaction.
Meta Description: “Discover the top 5 T-Mobile warehouse tips to optimize inventory management, storage solutions, workforce management, technology integration, and performance metrics. Improve efficiency, reduce errors, and enhance customer satisfaction with these expert insights.” (149 characters)